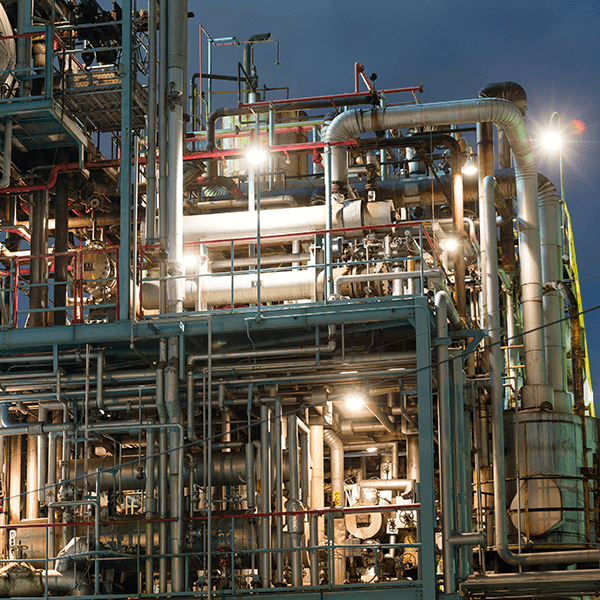
Leak testing is too often considered as an afterthought resulting in costly situations and solutions, especially in production systems. Leak testing is a topic that should be discussed and considered at the design phase of production, leading to cost reductions and quality improvements.
Why Should You Consider Leak Detection?
Leak detection can impact product performance, the safety of personnel and equipment, environmental restrictions with compensation claims, and more. Leak testing should be considered as a means of product verification and should be performed in the production process as early as possible.
The first consideration in leak detection is the acceptable level of leakage before it becomes harmful. Leak specifications are expressed in a number of ways: flow rate, pressure decay and weight loss. The flow rate is where we specify the maximum permissible loss of contents, pressure decay is when we quote the maximum permissible loss of pressure, and weight loss is where we are able to measure the mass of the substance lost. All specifications must have time consideration as well, and the process is not always straightforward. Over specification can be as harmful as underspecification.
Once specifications are decided, the next step is to determine how to perform the test. The first step is to consider a test method that simulates the working conditions in its most convenient form. Accurate simulation accounts for all the factors that influence leakage: working pressure, viscosity of the gas/liquid to be contained, and the material and structure of the component. Testing speed should match production to avoid bottle-necks and all relevant quality standards. The general idea is there are many ways to leak test, however, virtually all of these can be placed into four distinct categories: pressure decay, flow measurement, trace method, and product deformation.
Except for product deformation, gases, including air, are generally used as a leak detection medium even when the goal is to house a liquid. Gases are clean, dry and penetrate very small holes making it and its movements readily detectable. Other mediums are through light, sound and a variety of other forces to help with leak testing.
Instrumentation Considerations
Once the method of leak detection is selected, the types of instruments and manufacturers have to be chosen. Each having its advantages and disadvantages, care needs to be taken to choose the right level of sensitivity, speed of response and the correct degree of immunity to external effects. Whatever method chosen, the product needs to be held steady during the test and ensure the connections between the component and the test instrument are made leak-tight in themselves, aka fixturing. Fixturing requires a lot of care and expertise since most of the problems found with a leak detection system result from poor connections.
Leak Detection Applications
There are a variety of applications valuing the use of leak detection systems, such as chemical plants, wastewater treatment, oil & gas, manufacturing and more. For example, the food and beverage industry implements leak detection systems due to risks of processes to maintain quality control and product preservation. Refrigerating and cooling systems also present a risk since they utilize pressurized ammonia, leading to serious side effects if leaked. Wastewater treatment centers must be wary of asphyxiants due to confined environments, leaving workers in spaces of high exposure if a leak were present.
Oil and gas applications involve several manufacturing processes requiring leak detection systems. Between offshore drilling or the production of gasoline, the exposure of the gases can compromise the safety of those in the refineries. Leak detection systems vary in this industry due to the various chains in oil and gas, making it essential to have the right system in place. Chemical plants, specifically chemical storage and chemical manufacturing, are one of the largest users of leak detection systems due to the variety of gases and toxins within the plant. This application utilizes fixed and portable detection systems due to the high risk of exposure, resulting in the difference between life and death.