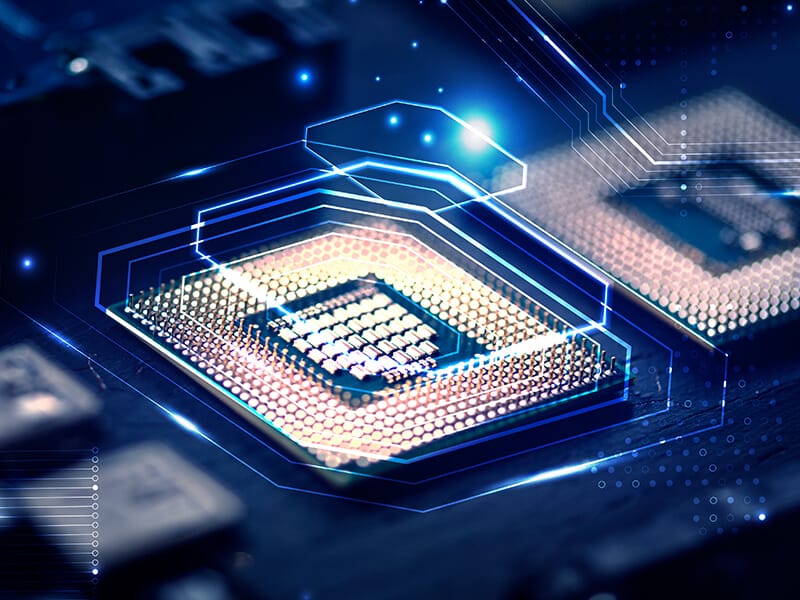
Semiconductor Guide – Role of VOCs in fabrication, worker safety and community exposure
Semiconductors have been playing an ever-increasing role in our life since their development in the 1960’s.
Semiconductors have changed the way we live and will continue to play a key role in our future. As the number of facilities increase the potential for harmful emissions increases and with the availability of abatement systems with live VOC monitoring, they can be proactively controlled. Worker health and safety is also of paramount importance and wearable VOC detectors can be used to protect workers from short term and long-term VOC exposure.
Role of VOCs in Semiconductor Fabrication and Worker Safety
Semiconductor devices are created via various fabrication processes whereby electronic circuits are gradually created on the surface of semiconducting materials called wafers. All these processes are performed in specialised technologically advanced multibillion dollar facilities known as Fabs.

”Whilst many VOCs have minimal adverse effects on health and the environment, some are harmful. Health effects include eye, nose, and throat irritation from short term (acute) exposures and long-term (chronic) exposure to very low concentrations may cause damage to your liver, kidneys, central nervous system, as well as cancers.
Controlling VOC Emissions
The semiconductor manufacturing industry is one of the potential major sources of air toxics or hazardous air pollutants (HAPs). The major emission sources are wet chemical stations, coating applications, gaseous operations, photolithography and packing processes. Industrial emissions are tightly regulated. In the US the National Emission Standards for Hazardous Air Pollutants (NESHAP) require all semiconducting manufacturing facilities meet emission standards reflecting the application of the maximum achievable control technology (MACT), and similar approaches are taken in Taiwan, Korea, Japan, China and elsewhere. VOC abatement technology is continuously improving, and a two-phase approach is usually adopted;
i) removal at source
ii) terminal prevention.
In the first phase various scrubbing technologies are used depending on the type of chemicals present including adsorption on carbon beds.
Health effects associated with benzene
The difference in harmful short term and long-term concentrations are considered here in reference to benzene. Short term exposure up to 50 ppm can result in headaches and fatigue, 1500 ppm serious illness, 7500 ppm threatens life, 20,000 ppm causes depression of the central nervous system, cardia arrhythmia, respiratory failure, and death. Whereas long term exposure to only 5 ppb (over 1000 times lower) can significantly increase the lifetime risk of leukaemia. It is estimated that occupational cancers are a leading cause of work-related death worldwide.
According to a study in Great Britain over one year, 5% of cancer deaths (8000) were attributable to occupational exposure.
– Royal College of Physicians
Download Our FREE Guide
“Semiconductor Guide – Role of VOCs in fabrication, worker safety and community exposure”
Huge volumes of VOCs are used, produced, and emitted throughout the manufacturing cycle of semiconductors. Some of the VOCs used and produced are known to be harmful to humans and there has been several reports of cancer outbreaks in facilities in the USA, UK and Korea over the last decade, with ongoing debate if there is a link2-4. There is also concern as semiconductor manufacturing increases, emissions of VOCs which can significantly deteriorate air quality in surrounding suburbs, will also increase.