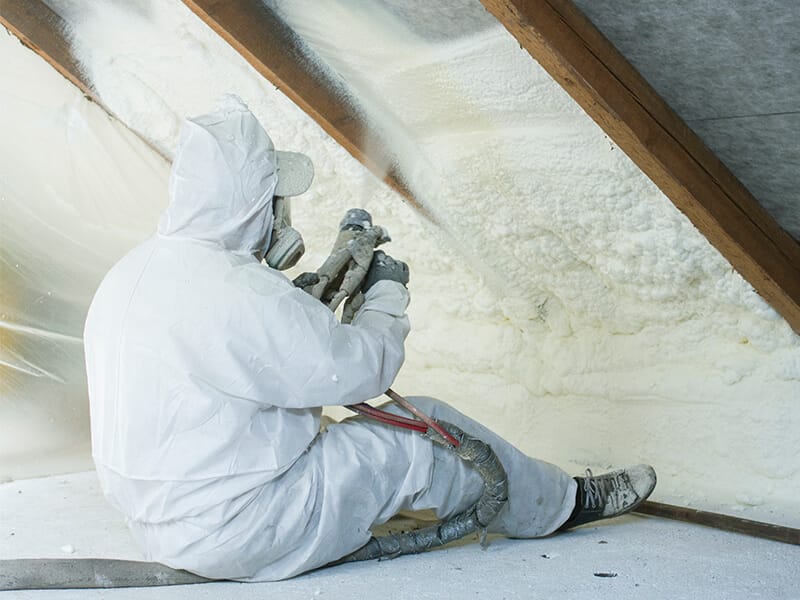
Detecting Propylene Oxide
Formula: C3H6O | CAS: 75-56-9
Protecting both people and the environment whilst meeting the operational needs of your business is paramount and if you have operations in the UK you will be well aware of the requirements of the Control of Substances Hazardous to Health (CoSHH) regulations and likewise the Code of Federal Regulations (CFR) in the US.
Similar legislation exists worldwide, the common theme being an onus on hazard identification, risk assessment and the provision of appropriate control measures.
Using propylene oxide in the manufacture of foam rubber
Market Growth | Manufacturing | Detection
The global polyurethane market size was estimated at USD 65.5 billion in 2018, with construction accounting for over 25% of the market and furniture and interiors just over 20% in terms of revenue as well as volume. Asia Pacific is now the leading regional market due to key players BASF and Dow moving production to countries like China and India. Europe follows as second largest with growth occurring in both the Central and South American and Middle East and African markets.
– Grand View Research
”Polyurethane foam rubber can be found in a wide range of every day applications ranging from wall insulation and appliances to car seats and furniture. It is created using a blowing agent such as isocyanate to facilitate the creation of gas bubbles in a plastic. Foam can be either flexible or rigid. Rigid foam or closed cell foam created using densely cross-linked polymers is used mainly as insulation for building or in refrigeration. Whereas flexible foam which can be produced in both high and low densities is used in applications such as furniture cushioning, mattresses and pillows.
Polyurethane foam rubber
A variety of materials are used to produce polyurethane foam rubber. Including monomers (molecules that can react with other molecules to form polymers), prepolymers (the intermediate state of a monomer before polymerisation) and stabilisers which protect the quality of the polymer itself.
Detecting diisocyanates
Diisocyanates are one of the key reactive materials used to produce polyurethane. The most commonly used in foam production are toluene diisocyanate (TDI) and methylene diphenyl diisocyante (MDI). MDI is used in the manufacture of rigid foams whereas TDI is used in applications where flexible foam is used such as furniture and bedding.
The dangers of propylene oxide
With an established 8 hour permissible exposure limit of 20 ppm by the Occupational Safety and Health Administration (OSHA) in the US continuous monitoring is vital to ensure a safe working environment.
Propylene oxide is an extremely flammable, highly volatile, colourless gas. Short-term exposure has been known to cause eye and respiratory tract infections, skin irritation and has even been found to be a mild central nervous system depressant in humans. Although not believed to be a threat to humans it has also been found to cause tumours in rodents following ingestion in inhalation exposure.
Download our FREE Guide
“Using propylene oxide in the manufacture of foam rubber”
The using propylene oxide in the manufacture of foam rubber guide which can be downloaded below provides the reader with an in-depth balance of knowledge covering the global polyurethane market size and why this product is used in such a mass range of applications. You will also discover the best way in monitoring Methylene diphenyl diiscocyanate (MDI) and monitoring Toluene Diisocyanate (TDI) which are the main reactive materials used to produce polyurethane.